Premix: Confidence in quality
Although the process of making a premix seems to be easy compared to the production of pelleted compound feed there is more to it than meets the eye. A multitude of micro ingredients with different physical and chemical properties have to be dosed in exactly the right quantities and mixed together in order to create a free flowing, non-reactive, dust free, nonhygroscopic and homogenous blend and it does not stop here. By the time the blend is used in a feed mill or by a home mixer it still needs to be homogenous and free flowing. It is essential that ingredients, like vitamins, are still present in the feed after the production process.
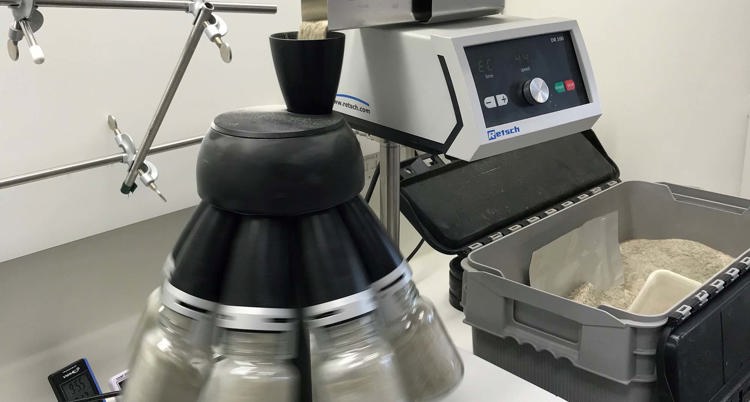
Vitamins
Vitamins are sensitive to degradation. Several factors can have a negative impact on the stability of vitamins: light; presence of oxidizing or reducing agents; heat; humidity; acidic- or an alkaline environment. The sensitivity towards these factors varies. Especially vitamin A, K, B6 and B1 are sensitive. Therefore vitamin producers improve stability while maintaining good digestibility, for example coated vitamin A and biological activity like vitamin E-adsorbate. At Koudijs we know that the quality of vitamins of different suppliers can be different and can change over time e.g. due to the ban on ethoxyquin. Our dedicated, international team of experts leads an extensive QA/QC monitoring program and continuously studies the quality of the products.
Vitamin A as an example
The last 2 years vitamin A has been under increased scrutiny due to the ban on the use of ethoxyquin as an antioxidant in the coating of vitamin A. It is well known that producers were forced to redesign their vitamin A, possibly leading to new differences between suppliers. Recently Koudijs conducted an extensive research project where 7 different product/supplier combinations of pure vitamin A were tested. These products were also tested in 3 different premixes with different compositions and a varying levels of choline chloride, trace elements and carriers. All products and premixes were tested at day of production (t=0); and at 3, 6 and 9 months. The expected level of vitamin A in the 0.5% premix was 2 million IU/kg premix. The results of the two most stable and 2 least stable pure products are displayed in figure 1. In figure 2 the results of 2 premixes with the highest and 2 with the lowest recovery rate are displayed.
Large differences in results
Results in figure 1 are expressed as a relative value compared to the first measurement at day 0. By doing so, the effect of possible overdosing of vitamin A in the pure product
is taken into account. Recovery rates of the pure product at t=o varied from -8% to +10% with an average of 100.8% compared to the values of the supplier specifications. It is clear from figure 1 that there are substantial differences between different supplier/product combinations. From the results in figure 2 it is clear that a stable, pure product does not necessarily mean that it is also the most stable product in a premixture. A possible explanation can be that the coating of a certain product is not strong enough to withstand the abrasive process of premix production. Another possibility is that the vitamin A is not stabilized enough with antioxidants like BHT and that vitamin A is
partly oxidized.
Conclusion
It is clear that there is variation in the level of vitamin A in the pure products and in the stability of these pure products as well as in premixes. Therefore we conduct this type of research and continue to monitor vitamins for use in the premixes. Leading to the best price/quality premixes possible at any moment in time.